
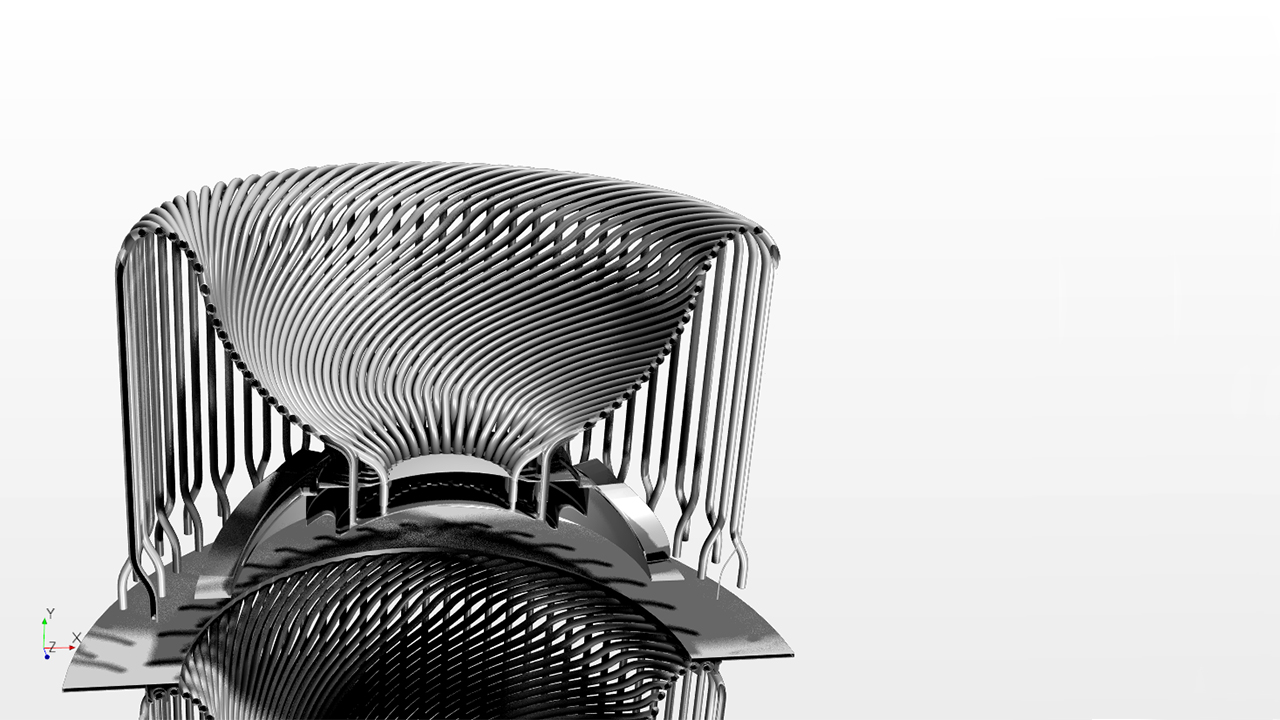
Indeed, we can easily execute the modal solver as a post-processing step using the solution field from steady-state RANS simulations. The approach avoids the need to export flow solutions to external tools for further analysis. This solver delivers engineers a rapid and convenient insight in thermoacoustic stability of the combustion systems. With Simcenter STAR-CCM+ 2206, we introduce an acoustic modal solver with the thermoacoustic n-tau model. This implies that a gas turbine combustor that is dynamically stable at a given equivalence ratio or flame temperature may be rendered dynamically unstable and vice versa as a result of hydrogen addition. Hydrogen enrichment has been reported to shift regions of thermoacoustic instabilities to lower equivalence ratios and flame temperatures. This phenomenon continues to be a challenging design consideration especially as the use of Hydrogen extends in the face of tightened emissions requirements. We consider thermoacoustics the coupling between pressure and heat release oscillations. In a file-based coupling, aerodynamic forces and moments from the blades stemming from transient aerodynamic simulations are automatically mapped to a beam representation throughout a full rotation. The structure dynamics solver in turn computes elastic blade deformations under those loads. The co-simulation autonomously iterates until the overall system is converged for both the structure and flow field enabling engineers to easily gain insights into the complex aeroelastic behavior of rotors. The new workflow is automatically linking and mapping to all common industry-standard rotor blade structural mechanics solvers, such as RCAS, CAMRAD II, DYMORE, or Flightlab with the ability to adapt to other software tools. Simcenter STAR-CCM+ 2206 offers a fully automated rotor blade aeroelasticity workflow that provides a high-fidelity solution with minimum user effort.

Hence, to increase the performance of those rotors while reducing vibration and noise, high-fidelity aeroelastic simulations are a key enabler for Computational Fluid Dynamics (CFD) engineers. Applications such as helicopters, urban air mobility vehicles, and wind turbines heavily rely on accurate predictions of the complex interaction between aerodynamics forces and structural responses of their rotor blades.
